Table of Contents
Related articles
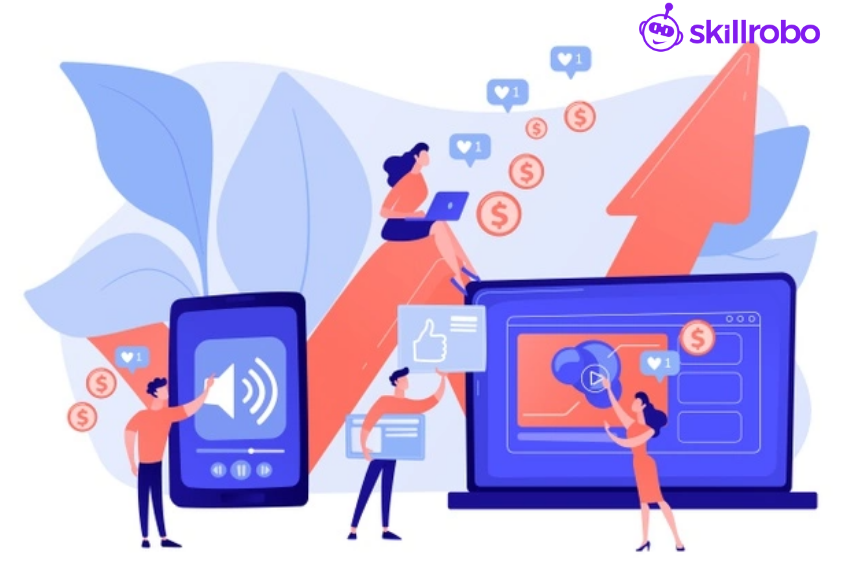
According to the latest report by the Bureau of Labour Statistics, over 45,000 positions in the non-durable goods manufacturing industry remained unfulfilled as of September 2021. For manufacturing companies to fill open positions in this candidate-driven market, they must be open to adopting technology-driven hiring tools like online production skills assessment tests and job simulations. Candidates need to be steeped in technical skills and show interest in continuously upgrading skills and competencies. Production skills assessment tests evaluate the candidate’s skills and cognitive ability to find the right fit.
6 Most Important Skills for Production Employees
While every production or manufacturing job will vary slightly in terms of the necessary background, expertise, and skills, most candidates seeking employment in this field need to develop the following skills:
1) Attention to detail: focusing on each component of the product or item while ensuring that it is properly assembled and packed is key to maintaining the quality of goods produced. The ability to focus on details is vital for success.
2) Critical thinking: production issues are common during manufacturing. The production team must be able to think through the issue and resolve it without much disruption to the production workflow. The ability to quickly identify the problem enables production personnel to perform their jobs efficiently.
3) Communication: regardless of the role played by the candidate on the production floor, the ability to communicate clearly and effectively is a must for production employees.
4) Computer usage: production and manufacturing roles require candidates to have good knowledge of computer and design related software like CAD or similar software.
5) Reliability: most of the manufacturing and production roles are autonomous, with occasional supervision by managers. After initial training on the job, employees are trusted to perform their tasks effectively and reliably.
6) Maintenance and repair of machinery: manufacturing and production personnel need to have good knowledge of how machines function. This knowledge enables them to handle machine repair and maintenance independently.
Roles in the Production Function
The Roles in the production function vary depending on the type and scale of business. The common production roles are listed below.
- Assembler: fabricators or assemblers put together various parts to get the finished product. Assemblers also assemble finished products and make them ready for quality inspection and packaging. They may do it manually or use machines to assemble parts.
- Machinist or operator: maintenance and operation of machines is the primary work of a machinist. They must be able to work on mechanically operated and computer-operated machinery.
- Production scheduler: production workflows must run as per pre-set schedules so that production goals are achieved. Production schedulers are tasked with creating and maintaining production schedules and ensuring that production workflows are not interrupted. They also need to ensure optimal resource utilization identify production bottlenecks and resolve them.
- Production manager: production managers are in charge of overseeing the day-to-day operations at manufacturing plants. They need to ensure that production workflow is uninterrupted and runs as per schedule, production issues are resolved immediately, and skilled candidates are hired for junior roles in production.
- Quality Control Inspector: the finished goods are inspected by quality inspectors for any hazards, deviations, or defects. Having good product knowledge helps perform QC inspection efficiently.
Appropriate educational background, job experience, and skills are required to perform various roles in the production function.
Challenges in Hiring for Production Roles
Hiring candidates for working in the production department needs to be done after careful evaluation of various skills and competencies. Wrong hires can cause disruptions in the production workflow, which eventually affects business outcomes. To maximize productivity, every business needs effective planning that covers a wide variety of activities that ensure the availability of human resources, production materials, and equipment. Employees working on the production floor need to have the skills described in the section above. The common challenges in hiring production personnel are:
- Attracting the right candidates: the scope of manual hiring processes is limited to attracting and screening a limited number of candidates.
- Engaging qualified candidates: engaging candidates with the right skills is a challenge through conventional hiring methods.
- Quick and effective hiring against job positions: Manual hiring processes are not effective for hiring production personnel quickly.
- Inadequate manual hiring processes: Manual hiring processes cannot scale up to large-scale requirements for production roles.
Production skills assessment tests on the other hand provide an accurate and holistic evaluation of the candidate’s skills and behavioral tendencies. A manufacturing skill assessment test comprises job-related evaluation, psychometric evaluation, logical and analytical reasoning ability, and communication skill evaluation. Thorough evaluation of candidates ensures superior performance on the job and seamlessly fits into the work culture.
Features of Production Assessment Test
Production skill assessment tests are designed to evaluate a candidate beyond just technical skills to assess their ability to fit into the work culture and to deal with work-related challenges. Skillrobo is a pre-employment skill assessment software that provides fully customizable skill assessment tests that can be used for evaluating candidates for diverse roles across various industries. Online production assessment tests like the ones provided by Skillrobo enable effective skill evaluation of candidates for different roles in the production department.
Key features of pre-employment skill assessment tests are:
- Customizable skill library – the skill test can be customized according to the role for which the candidate is being hired.
- Fraud and cheating prevention – the secure test environment prevents malpractices during the test. The online activity of the candidate is constantly monitored throughout the test.
- Reporting and analytics – instant reports and analytics of the candidate’s performance are made available to the hiring team to make informed recruitment decisions.
- Online administration – the hiring team can conveniently share the test link via email to the candidate. The candidate can take the test from anywhere at a convenient time.
Conclusion
Hiring highly efficient and skilled production personnel improves the quality of production and operational efficiency. Pre-employment skill assessment software empowers the recruitment team to make the right hiring decision by enabling holistic candidate evaluation. Online production assessment tests from Skillrobo are tested and trusted ways to find the right candidate for various production roles. Visit us to know all about production skill assessment tests.
Sign up for the free trial of Skillrobo and experience efficient hiring.
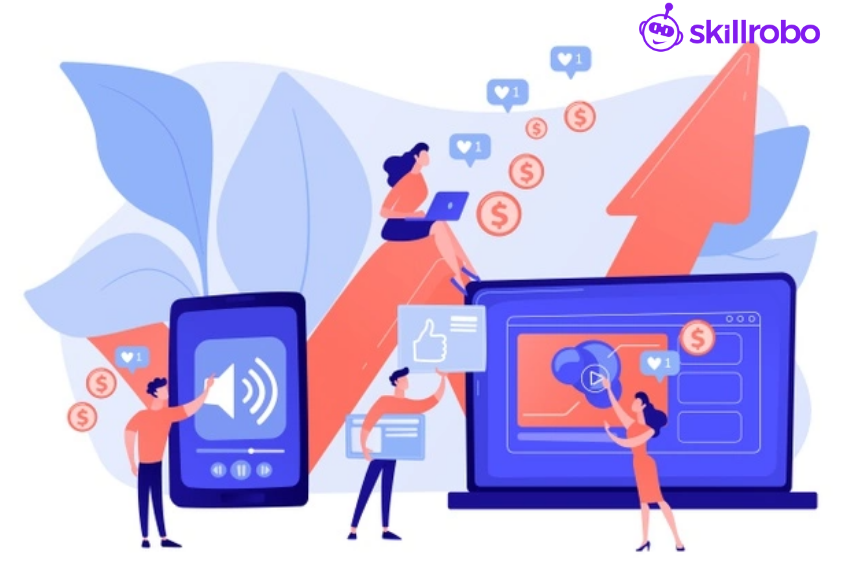
According to the latest report by the Bureau of Labour Statistics, over 45,000 positions in the non-durable goods manufacturing industry remained unfulfilled as of September 2021. For manufacturing companies to fill open positions in this candidate-driven market, they must be open to adopting technology-driven hiring tools like online production skills assessment tests and job simulations. Candidates need to be steeped in technical skills and show interest in continuously upgrading skills and competencies. Production skills assessment tests evaluate the candidate’s skills and cognitive ability to find the right fit.
6 Most Important Skills for Production Employees
While every production or manufacturing job will vary slightly in terms of the necessary background, expertise, and skills, most candidates seeking employment in this field need to develop the following skills:
1) Attention to detail: focusing on each component of the product or item while ensuring that it is properly assembled and packed is key to maintaining the quality of goods produced. The ability to focus on details is vital for success.
2) Critical thinking: production issues are common during manufacturing. The production team must be able to think through the issue and resolve it without much disruption to the production workflow. The ability to quickly identify the problem enables production personnel to perform their jobs efficiently.
3) Communication: regardless of the role played by the candidate on the production floor, the ability to communicate clearly and effectively is a must for production employees.
4) Computer usage: production and manufacturing roles require candidates to have good knowledge of computer and design related software like CAD or similar software.
5) Reliability: most of the manufacturing and production roles are autonomous, with occasional supervision by managers. After initial training on the job, employees are trusted to perform their tasks effectively and reliably.
6) Maintenance and repair of machinery: manufacturing and production personnel need to have good knowledge of how machines function. This knowledge enables them to handle machine repair and maintenance independently.
Roles in the Production Function
The Roles in the production function vary depending on the type and scale of business. The common production roles are listed below.
- Assembler: fabricators or assemblers put together various parts to get the finished product. Assemblers also assemble finished products and make them ready for quality inspection and packaging. They may do it manually or use machines to assemble parts.
- Machinist or operator: maintenance and operation of machines is the primary work of a machinist. They must be able to work on mechanically operated and computer-operated machinery.
- Production scheduler: production workflows must run as per pre-set schedules so that production goals are achieved. Production schedulers are tasked with creating and maintaining production schedules and ensuring that production workflows are not interrupted. They also need to ensure optimal resource utilization identify production bottlenecks and resolve them.
- Production manager: production managers are in charge of overseeing the day-to-day operations at manufacturing plants. They need to ensure that production workflow is uninterrupted and runs as per schedule, production issues are resolved immediately, and skilled candidates are hired for junior roles in production.
- Quality Control Inspector: the finished goods are inspected by quality inspectors for any hazards, deviations, or defects. Having good product knowledge helps perform QC inspection efficiently.
Appropriate educational background, job experience, and skills are required to perform various roles in the production function.
Challenges in Hiring for Production Roles
Hiring candidates for working in the production department needs to be done after careful evaluation of various skills and competencies. Wrong hires can cause disruptions in the production workflow, which eventually affects business outcomes. To maximize productivity, every business needs effective planning that covers a wide variety of activities that ensure the availability of human resources, production materials, and equipment. Employees working on the production floor need to have the skills described in the section above. The common challenges in hiring production personnel are:
- Attracting the right candidates: the scope of manual hiring processes is limited to attracting and screening a limited number of candidates.
- Engaging qualified candidates: engaging candidates with the right skills is a challenge through conventional hiring methods.
- Quick and effective hiring against job positions: Manual hiring processes are not effective for hiring production personnel quickly.
- Inadequate manual hiring processes: Manual hiring processes cannot scale up to large-scale requirements for production roles.
Production skills assessment tests on the other hand provide an accurate and holistic evaluation of the candidate’s skills and behavioral tendencies. A manufacturing skill assessment test comprises job-related evaluation, psychometric evaluation, logical and analytical reasoning ability, and communication skill evaluation. Thorough evaluation of candidates ensures superior performance on the job and seamlessly fits into the work culture.
Features of Production Assessment Test
Production skill assessment tests are designed to evaluate a candidate beyond just technical skills to assess their ability to fit into the work culture and to deal with work-related challenges. Skillrobo is a pre-employment skill assessment software that provides fully customizable skill assessment tests that can be used for evaluating candidates for diverse roles across various industries. Online production assessment tests like the ones provided by Skillrobo enable effective skill evaluation of candidates for different roles in the production department.
Key features of pre-employment skill assessment tests are:
- Customizable skill library – the skill test can be customized according to the role for which the candidate is being hired.
- Fraud and cheating prevention – the secure test environment prevents malpractices during the test. The online activity of the candidate is constantly monitored throughout the test.
- Reporting and analytics – instant reports and analytics of the candidate’s performance are made available to the hiring team to make informed recruitment decisions.
- Online administration – the hiring team can conveniently share the test link via email to the candidate. The candidate can take the test from anywhere at a convenient time.
Conclusion
Hiring highly efficient and skilled production personnel improves the quality of production and operational efficiency. Pre-employment skill assessment software empowers the recruitment team to make the right hiring decision by enabling holistic candidate evaluation. Online production assessment tests from Skillrobo are tested and trusted ways to find the right candidate for various production roles. Visit us to know all about production skill assessment tests.
Sign up for the free trial of Skillrobo and experience efficient hiring.